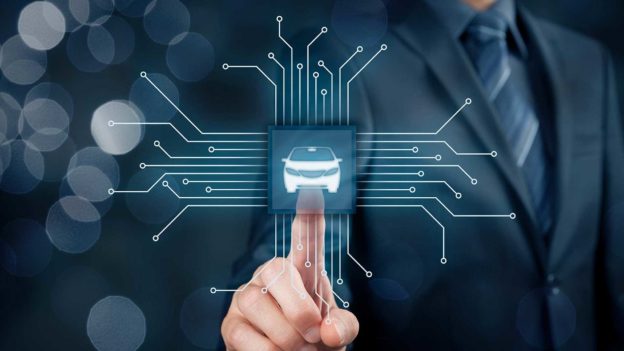
「2021 年汽車產業全面復甦,國際汽車供應鏈紛紛來台敲門,半導體業者難得的機會來了,產品零缺陷 Zero Defect 是一門檻,您準備好了嗎?」
因 COVID-19 疫情各國封城下,2020 上半年車用半導體市場大幅衰退,不過到了 2020 下半年,汽車的需求與生產情況好轉、現階段汽車庫存水位低、以及各國對於自駕車法規的逐步制定,將驅使 2021 年車用電子市場大幅成長。
宜特觀察,台灣半導體市場也沒有閒著,近期國際汽車供應鏈來台敲門,除了來搶晶圓代工產能,也順道了解台灣在地汽車零組件供應鏈,特別是未來電動車、ADAS、自駕車等普及,對於半導體的需求將會快速拉升,然而汽車電子產品的設計製造思維,不若是一般消費性產品「Time to Market」,必須以「Design for Reliability」品質為優先。
當越來越複雜的電子系統應用於汽車中,任一功能失效時,都有機會對駕駛、乘客、附近車輛以及行人引發難以預料的威脅。汽車電子的缺陷,不但對人身安全帶來潛藏危機,緊隨其後的召回事件也將使企業擔負昂貴的認賠責任。因此,減少及預防電子元件缺陷變得至關重要。
汽車製造商(Vehicle Maker)和一級系統供應商(Tier 1)為提高電子產品的品質和可靠性,要求電子元件故障率的等級降至十億分之一(Parts Per Billion;ppb),因此,在電子產品供應鏈中推行「零缺陷(Zero Defect)」的概念。
零缺陷(Zero Defect)如何做到?為了讓相關汽車電子供應鏈有所依循,美國汽車電子委員會(Automotive Electronics Council, 簡稱 AEC)推出一系列的汽車電子規範 (進一步閱讀: 六大重點,秒懂車用多晶片模組 AEC-Q104 規範),其中在2020年針對零缺陷(Zero Defect)推出新版 AEC-Q004 指導性方針(Guideline),此方針類似工具書的概念,主要針對 AEC-Q100(IC晶片)、AEC-Q101(離散元件)、AEC-Q102(離散光電元件)、AEC-Q103(MEMS)、AEC-Q104(多晶片模組)以及 AEC-Q200(被動元件)規範中未盡之處做補充。
本次宜特小學堂,將針對 AEC-Q004 基本觀念、與 Zero Defect 的六大類工具做一詳盡說明。
壹、基本觀念
AEC-Q004 對零缺陷(Zero Defect)提供一個策略架構(參見圖一),主要目標是將業界最佳的製程、方法和工具,或是元件供應商內部專屬的缺陷篩檢手法,運用在製程設計、產品設計、生產、以及產品/製造改善等階段,以達減少缺陷。
適用對象則包括,符合 AEC-Q100(IC晶片)、AEC-Q101(離散元件)、AEC-Q102(離散光電元件)、AEC-Q103(MEMS)、AEC-Q104(多晶片模組)以及 AEC-Q200(被動元件)規範的半導體產品。
▲圖一:Automotive Zero Defects Framework(圖片來源:AEC-Q004)
貳、Zero Defect 架構之應用
此架構提供了一套工具,半導體供應商可以利用這些工具來檢測、減少和消除缺陷。供應商可以與半導體元件使用者進行協議,考慮到有效性、易用性、可用性和成本等等,選擇架構中的工具加以組合,進而達成客戶對產品的期望與要求。
為達零缺陷的目標,此架構將工具分為六大支柱(參見圖二),包括一、產品設計階段(Product Design);二、製造階段(Manufacturing);三、測試階段(Test);四、應用及能力(Application and Capability) ;五、持續改善手法(Continuous Improvement Methods);六、問題解決(Problem Solving),分別使用於電子元件開發設計、製造、測試、產品應用、改善手法及問題解決等階段。以下內文針對各工具進行簡易說明。
▲圖二:零缺陷架構的六大支柱
一、產品設計(Product Design)
1.設計階段的失效模式與影響分析(Design Failure Mode and Effect Analysis,簡稱 DFMEA)
DFMEA 用於識別設計階段潛在的故障模式及其對系統與應用中產品的影響,評估風險指數「嚴重度(Severity)、發生度(Occurrence)、偵測度(Detection)」,確定可能的真因並採取控制措施,FMEA 亦為 IATF 16949 五大核心工具之一(參見圖三)。 (進一步閱讀: 了解三大面向,順利取得IATF 16949汽車品質管理系統證書)
▲圖三:IATF16949 五大核心工具
2.備援(冗餘)機制(Redundancy)
指具有相同功能之單元或組件的備用系統。基於失效安全的考量,用於無縫替換故障的單元或組件,延長系統順利運作到出現失效的時間。
3.內建自我測試(Built-in Self-Test,簡稱 BIST)
內建自我測試功能(BIST)是在積體電路中加入自我檢測的技術,一般使用於高複雜性的元件。在開發階段和批量生產中,利用該檢測電路測試元件之功能、參數或兩者,降低對外部自動測試設備(Automatic Test Equipment,簡稱 ATE)的依賴以及測試成本,並縮短上市時間(Time to Market,簡稱 TTM)。
4.可測試設計(Design for Test)
使用於高複雜性的元件,在合理的時間內測試盡可能多的節點(nodes),從而在測試過程中提供最大的故障覆蓋率。簡單來說,就是在量產前,利用測試程式(Test Program)去測試無法察覺或潛在的故障,如果測試能夠發現所有潛在的故障,其覆蓋率越高,IC 產出的錯誤(Bug)就越少。
5.分析設計(Design for Analysis)
為避免高複雜性的元件無法找到缺陷,從電路設計階段著手,允許直接觀察和控制嵌入式及底層電路,以便找出故障的電路及執行物性故障分析(Physical Failure Analysis;PFA)。
6.可製造性設計(Design for Manufacturability)
在電路設計上通過更大的設計餘裕度(design margins),使零件的製造更具可重複性和複製性,以減少製程缺陷對產品的影響,進而提高產品產量和質量。
7.可靠度設計(Design for Reliability)
可靠度設計可以提供預估元件可靠度壽命的能力。在不犧牲性能的前提下,透過電路、佈局或結構面來防止可靠度問題。
8.仿真模擬及模型建立(Simulation and Modeling)
仿真模擬是一種對最終產品或其一部分的功能和可靠性表現進行模擬的方法。該方法使用製程元素模型、封裝物理/材料模型及設計準則,驗證產品在整個生命週期中的功能性及表現。與僅在實際產品上進行驗證相比,仿真模擬可以提供更多樣的參數變化。
9.特性分析(Characterization)
藉由觀察元件的溫度、電壓、頻率、安全機制等參數特性,了解元件的製程屬性、表現、限制,用以建立該產品的製程規格限制及規格書。此部分亦符合 ISO26262 對於產品功能安全設計的要求。
二、製造(Manufacturing)
1.製程階段的失效模式與影響分析(Process Failure Mode and Effect Analysis,簡稱 PFMEA)
PFMEA 用於識別生產階段潛在的故障模式及其對系統與應用中產品的影響,評估風險指數「嚴重度(Severity)、發生度(Occurrence)、偵測度(Detection)」,確定可能的真因並採取控制措施,FMEA 亦為 IATF16949 五大核心工具之一。
2.變異統計分析(Statistical Analysis of Variance)
運用統計手法將製程中的變數(如:製程參數)進行分析,此變數會與產品的特定電性或其他參數有關。由數據中發現的變異性分可為系統性因素和隨機性因素。藉此方法調配製程參數或產品特性,以實現最佳的良率、功能或可靠性。
3.控制計劃(Control Plan)
控制計劃概述產品/製程的特性以及相關的製程變量,確保產品能力達到目標或標準值,且隨時間推移可保持其穩定性。例如 Cpk 是控制計劃中用於測量穩定性的一種方法。控制計劃包含遇到偏移時所需採取的措施,如:品質異常矯正執行計劃(Out of Control Action Plan,簡稱 OCAP)。
4.統計製程管制(Statistical Process Control)
統計製程管制(SPC)主要利用管制圖(Control Chart)與製程能力分析(Ca, Cp, Cpk)…等統計方法,即時監控產品的生產流程、蒐集資料,發掘製程中之異常,找出變異的原因、提出對策且立即改善製程,進而保持品質和參數穩定性。
5.批次驗收(Lot Acceptance Gates)
針對批次成品進行取樣測試,以確定該批產品是否適合進一步製造或出貨給客戶。
6.稽核-管理系統、製造過程和產品(Audits–Management System, Manufacturing Process and Product)
稽查或審核是否按照 IATF16949 等車用行業標準,確保品質管理系統、製程與產品檢驗相關規範的維持、發展及改進。
三、測試(Test)
1.零件平均測試(Part Average Testing)
一個用於設計、分析、控制製造和測試參數(電性或物理)的系統,以監控產品品質。利用緊縮規格以更嚴謹的品質提升可靠性,意即把分佈中的異常元件(outlier)從所有產品中剔除的統計方法(參見圖四)。
▲圖四:Guidelines for Part Average Testing(圖片來源:AEC-Q001)
2.統計良率分析(Statistical Bin Yield Analysis)
2.統計良率分析(Statistical Bin Yield Analysis)
利用統計方法,在晶圓測試(wafer sort)階段統計、分析特定關鍵測試參數(Bin),設定某一個失效參數(fail bin)的數量及良率的條件,用以做品質卡關的動作,確保產品的品質和可靠度。
3.數據收集、存儲和檢索(Data Collection, Storage and Retrieval)
數據資料的測量、存儲、歸檔及檢索。可用於解決可靠性與產品製造相關的問題。快速的數據取用性將加快問題的控制及改善,並允許快速的風險評估,成為品質改進的基準。
4.篩選(Screens)
測試篩選是用來確保產品表現及穩健性(Robustness)的工具,防止由缺陷所引起的故障機制。
四、應用及能力(Application and Capability)
1.行業標準(Industry Standards)
提供一標準測試方法適用於供應商及用戶,並針對設備、製程和材料提出行業基準。
2.環境應力測試(Environmental Stress Testing)
利用測試驗證找出產品在設計、製程或封裝中的弱點,確保產品滿足供應商和用戶之間對於品質和可靠度的要求。測試驗證透過物理、機械、電氣和環境應力等加速手法,使潛在磨耗和缺陷問題提早浮現。
3.應力強度分析(Stress-Strength Analysis)
應力強度分析是一種使用「測試至失效(Test to fail)」的原理,並分析所得到的故障分佈數據,進而決定對於特定應用之設計及製程餘裕度(margin)。
- 系統工程(Systems Engineering)
此為系統設計與使用者應用面保持一致的方法。系統工程的實踐涉及將用戶需求轉換為系統要求,然後可以通過建構和設計來實現。要實現零缺陷目標,需要考慮系統級結構,以納入可靠度設計(Design for Reliability,簡稱 DfR)、可製造性設計(Design for Manufacturability,簡稱 DfM)和測試設計(Design for Test,簡稱 DfT)。在開發的早期,產品規格和驗證計劃必須確保滿足系統要求。此外,具有功能安全(Functional Safety)要求的產品已定義了包含系統工程的標準,如:ISO26262 V model(參見圖五),以達到各車輛安全完整性等級(Automotive Safety Integrity Level,簡稱 ASIL)相應的功能安全設計之故障指標(Fault Metric),及診斷覆蓋率(Diagnostic Coverage)允收標準。
▲圖五:V model (圖片來源:ISO 26262: 2018)
5.產品降額定(Product Derating)
小於製造商/供應商指定之規格或操作範圍內使用產品的方式。將元件上的電、熱、機械應力降低到低於額定值的水平,用於延長元件的壽命、增加可靠性,有助於保護元件免受意外的應用異常。
五、持續改善手法(Continuous Improvement Methods)
1.晶圓級製程監控(Wafer Level Process Monitoring)
於製造初期快速測試特定的故障機制(如:TDDB、HCI、BTI、EM等),進行修復、報廢有缺陷的晶圓或批次,及早發現潛在問題,透過分析與控制特定的故障機制,為分析和篩選提供統計參考依據。
2.製程及產品改進(Process and Product Improvements)
為解決根本問題(Root Cause)或基於製程與設計的持續改善,對材料、製程或嵌入式軟體(硬體)進行更改,以提升產品功能、產量及可靠性,但應注意風險管理,例如:FMEA 更新。
3.產品可靠度監控(Product Reliability Monitoring)
定期對代表性樣品進行可靠度測試,目的是監控製程是否發生偏差,造成產品的缺陷,提供解決方案並進行修正,以降低後續生產產品發生異常之風險。
4.缺陷監控(Defect Monitoring)
實現零缺陷取決於所有供應商在半導體產品層面的共同努力,而達成零缺陷的成功關鍵在於監控與消除缺陷。缺陷可能會受到許多不同的影響,包括製程、設備、環境和人為因素。故缺陷監控是在整體生產流程的關鍵階段中,定期觀察或檢查生產材料品質的過程,含括電氣量測、目檢…等。藉此提高良率和可靠性,以降低早期現場故障,避免能夠輕鬆解決的問題愈演愈烈。
六、問題解決(Problem Solving)
1.問題解決技巧(Problem Solving Techniques)
通過識別真因(Root Cause)、遏制和糾正產品及製程問題,驗證問題是否得到解決以及防止問題再次發生。另外還可以作為報告工具,為客戶記錄問題,例如:8D 報告、魚骨圖(Fishbone)、失效樹分析(Fault Tree Analysis)等。
2.故障分析程序(Failure Analysis Process)
當汽車製造鏈中的任何層級發生故障時,終端客戶可以要求其供應商進行故障分析(Failure Analysis;FA)。故障分析是確認故障原因的過程,此過程中涉及收集和分析大量數據,找出明確的故障原因後,採取相應的遏制和糾正措施,以防止再次發生。分析程序應先由非破壞的電性故障分析(Electrical Failure Analysis;簡稱 EFA)著手,確認故障後再進行破壞性的物性故障分析(Physical Failure Analysis;簡稱 PFA)。
參、結語
與以往相比,現今的汽車工程環境中,是由半導體元件與高複雜度的系統相互依存在一起,每輛車在技術上都更加先進。因此,減少缺陷對於所有製造商來說都是極其重要的努力標的,但採取「零缺陷計劃」顯著提高了技術、品質及成本等門檻。
零缺陷的產生來自於預防的概念,如果選擇零缺陷策略,那麼運作及思維模式必須變化,從各自獨立運行或是溝通甚少的單位,轉變為跨部門的網絡式系統思維,串聯並共享資訊,以更全面的方法來解決缺陷問題。
宜特建議往零缺陷方向努力的供應商,除了符合 AEC-Q 系列規範外,在設計階段可運用 ISO26262 對於功能安全設計的要求,於製造與出貨階段,符合 IATF16949 以降低品質變異。宜特擁有汽車電子可靠度驗證與體系面輔導服務的豐富經驗,若您有車規驗證、ISO26262 及 IATF16949 輔導需求,想要更進一步了解細節,歡迎洽詢 +886-3-579-9909 分機 1068 邱小姐│Email: marketing_tw@istgroup.com
(圖片來源:宜特科技)