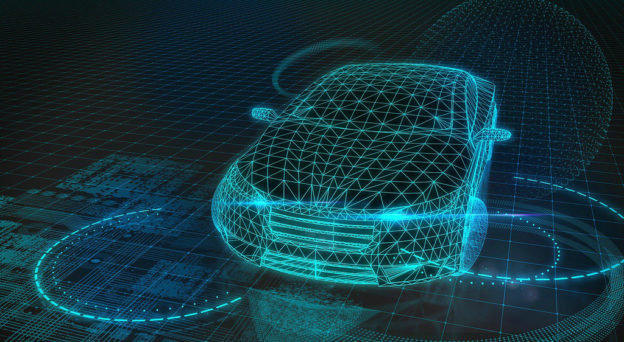
自從蘋果公司(Apple Inc.)於 2017 年首次在 iPhone X 推出 Face ID 人臉辨識功能,取代了行之有年的 Touch ID 指紋辨識之後,各家手機廠商才開始注意到這個以往只有在電影場景裡出現的黑科技。這個讓電子產品猶如擁有視覺般,得以辨別使用者立體輪廓的就是 3D 感測模組,而其中最關鍵的元件就屬近期紅透半邊天的面射型雷射–VCSEL。
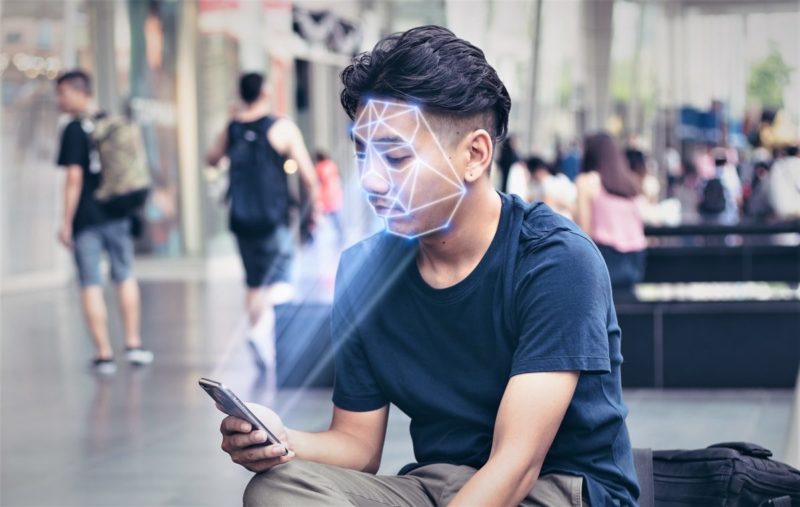
▲ 圖一 人臉辨識功能(Source:Shutterstock)
VCSEL 是 Vertical Cavity Surface Emitting Laser 的縮寫,意即「垂直共振腔面射型雷射」(註1)。自從 1962 年的第一個半導體雷射二極體展示之後,陸續有類似結構的元件發表。而現代公認的 VCSEL 發明者則是日本東京工業大學的伊賀健一(Kenichi lga)教授,他於 1977 年在實驗室筆記本上畫出了第一個 VCSEL 圖形(圖二),並且於 1979 年以液相磊晶(Liquid Phase Epitaxy, LPE)技術製備出 InGaAs/InP 材料的 VCSEL,開啟了後續一連串的學術研究及商業應用。
▲ 圖二 手繪 VCSEL 圖形(Source:銀月光科技)
人類視覺 vs. 機器視覺
說起人類視覺與機器視覺最大的差異,在於人類能將看到的畫面直接解讀成具有深淺的三維空間訊息,機器視覺則是針對獲取畫面的每一個像素進行編碼,只能得到二維平面影像,而沒有物體遠近的訊息。因此,3D感測技術是提升機器視覺能力,甚至進一步賦予機器與環境互動及行動化能力的關鍵。
3D 感測模組包含有「發射源」及「偵測器」兩個部分,偵測器大致區分為 Si based CMOS 以及 III-V 類型,如 InGaAs 類的材料或是量子點等技術,根據不同的接收波段選擇適用的偵測器。發射源目前的主流是使用紅外光源(Infra-Red, IR),因為相較於可見光,紅外光源有更佳的訊噪比(Signal-to-Noise Ratio, SNR)。而由於紅外光波段有好幾個適合的波長,像是近紅外光(Near-IR, NIR)的 850nm、905nm、940nm 波段,短波紅外光(Short-Wave IR, SWIR)的 1,350nm、1,550nm 波段,因此目前各家廠商各自選擇不同的波段及發展相對應的模組。
3D 感測模組:紅外光發射源,三大元件結構大比拚
若以元件結構來區分紅外光的發射源,則可以分成三大類,如圖三所示,包括:1. 發光二極體(Light-Emitting diodes, LED)、2. 邊發射雷射器(Edge Emitting Laser, EEL),以及3. 垂直共振腔面射型雷射 VCSEL。雖然 LED 及 EEL 仍有價格上的優勢,但考量元件穩定性及量產性,VCSEL 能在更大的溫度範圍內維持波長的穩定性,也更容易進行陣列封裝。綜整比較,VCSEL 在高輸出功率、高轉換效率和高品質光束各方面都勝出,因此被廣泛應用在 3D 感測的應用領域。
▲ 圖三 3D 成像模組的紅外光源種類(Source:閎康科技)
VCSEL 新發展—汽車自動駕駛系統
VCSEL 除了在光通訊及智慧手機的感測光源應用之外,汽車自動駕駛系統的關鍵感測元件-光學雷達(又稱光達、LiDAR),則是下一個帶動 VCSEL 發展的重大應用。LiDAR 全文為「Light Detection and Ranging」,是利用雷射感知探測距離的方法,藉由發射雷射脈衝並收集前方物體反射回來訊號的時間差,來進行距離的推算,達到測量距離的目的。而車用光達系統利用同時發射並處理多點雷射脈衝的數據,就能構築成一個具有深度資訊的 3D 環境模型,再透過識別道路標誌、汽機車、行人等靜態及動態物體的位置動作,達到自主感知的目的,幫助車輛檢測路徑中的障礙物,進而實現避障、煞停、路徑規劃等自動駕駛的應用。此外,深度感測系統亦可安裝於車內,進行座艙內監測和乘客手勢感測,達到駕駛輔助與提升乘車舒適度。
汽車產業一直朝著搭載高級駕駛輔助系統(Advanced Driver Assistance System, ADAS)的智能自駕車方向發展,汽車搭載光學雷達和深度感測系統已是必然的趨勢。而 VCSEL 元件和模組要應用在車載領域,就必須通過車規 AEC-Q10 2的高標準驗證,範圍涵蓋晶圓製造、元件封裝、電性與光學功能及可靠度驗證等。在車用元件驗證的範疇裡,著重在如何有效降低失效率,其終極目標則是 AEC-Q004 所要求的零失效。整體車用光學離散元件驗證流程如圖四,藉由應用 6δ、統計製程控制 SPC(Statistical Process Control)等品管手法來有效控制失效率,並且藉由提高驗證樣品數量來保證更低的失效率。
▲ 圖四 AEC-Q102 驗證流程圖(Source:AEC-Q102)
嚴格的車規驗證耗時漫長?閎康科技建立一站式服務
VCSEL 元件的車用可靠度驗證,包含了環境應力試驗、加速壽命模擬試驗、封裝強度試驗、結構強度可靠度及光學電性驗證等五大項試驗。為了縮短驗證時間,閎康科技建立了 One-Site Service 的一站式服務,特別引進 VCSEL 光學特性量測設備(圖五),在 AEC-Q102 驗證過程無須再送回客戶端執行功能驗證,直接在閎康內部即可完成,減少元件來回運送時間,進而縮短整體驗證時間。
▲ 圖五 VCSEL 光學特性量測設備(Source:閎康科技)
閎康科技在 AEC-Q 車用電子驗證有非常豐富的經驗,並已輔導多家客戶成功通過嚴格的車規驗證。對於希望進入車用市場的客戶,閎康科技能夠提供全方位車用驗證服務,亦可進行整體規劃方案,包括 AEC-Q100、Q101、Q102、Q104、Q200 等,協助客戶順利取得進入車用市場的門票,讓產品能安心安裝在汽車上,成為車廠供應鏈的一員。
▲ 圖六 閎康科技全方位車用驗證服務(Source:閎康科技)
註1:取自國家教育研究院頒布雙語詞彙、學術名詞暨辭書資訊網。
(首圖來源:Flickr/Automobile Italia CC by 2.0;資料來源:閎康科技)