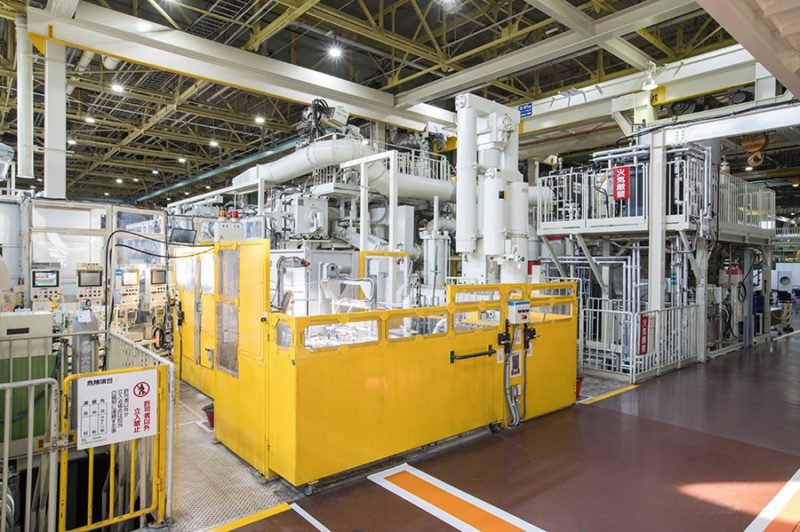
不久前 Toyota 揭示了他們提升電動車競爭力的重大革新,在上週舉辦的 Toyota 造物工作坊裡,進一步展示了更多細節,其中最讓我們關注的就是電動車的生產方式改變,確實從特斯拉身上學到不少招式。
為了打造出更具產品競爭力的次世代純電車,在新任社長領導下,Toyota 決心大幅改造他們的生產線,儘管在名稱上,依然維持所謂「TPS」豐田生產系統的哲學,但從技術上來看,確實從當前電動車成本之王特斯拉身上學習了很多。
撇除看起來難度極高的全固態電池,Toyota 展示的新造車製程裡,至少有兩項跟特斯拉直接相關。第一項是最近非常熱門的「一體式壓鑄」,簡單來說,是將原本複雜的汽車零件,盡可能的使用巨大的壓鑄機,一體化製作,省去組裝、焊接、運輸零件的過程和成本,特斯拉在這方面領先業界,進而創造出巨大的成本優勢。
日本老師傅的壓鑄活
Toyota 則在他們的明知(Myochi)工廠,也導入了一體式壓鑄設備,根據官方說法,新世代電動車將會有三分之一的車身使用一體式鑄造,所需的製作時間是短短的 3 分鐘。同樣的成品,傳統製程需要 86 個零件、33 項步驟和一個小時的工作時間。
特別的是,Toyota 表示一體式鑄造需要定期更換鑄造模具,通常需要停機 24 個小時,然而豐田擁有長年累積的低壓鑄造經驗與模具專業知識,這些頂尖匠人設計出一種新的模具,可以在 20 分鐘左右完成模具更換,大幅節省了生產時間。另外,日本模具的精準度,更讓一體式鑄造的良率更加提升,減少瑕疵情形,這一點只要是對機械製造有所涉獵的朋友應該都會同意。
數位孿生 Digital Twin
第二項跟特斯拉學習的則是 Digital Twin,翻譯成數位雙子、數位孿生等不同名詞,這項技術也不是特斯拉獨有,但卻是他們很早就開始導入的生產原則。簡單來說,在這個原則下,每一個實體產品,都有它的虛擬版本,能夠追蹤模擬實體產品的情形,更快速進行改動,來解決發現的問題。
Toyota 在貞宝工廠(Teiho),導入了兩種形式的數位雙生系統,第一是製造設備的數位孿生,將造車所需的新設備先建成 3D 模型,讓工人在數位環境中試用,提前發現問題進行改良,再將修正版本快速導入生產線上,就能縮短設計到生產的前置時間至少一半。
第二則是將現有的舊生產設備建立新的 3D 模型,如此就能更好的與新設備協作改良,同時也可以更快速的調整舊設備,另外也讓舊設備的自動化操作變得更容易,減少人工操作的時間,使得生產效率提升三倍。
Toyota 的三節式造車
最後展示的則是他們新的次世代電車生產概念,將車輛分為前、中、後三段分開製造,讓工人可以在開放環境下工作,搭配自走式生產模式,提高工作效率。
Toyota 打算將自動駕駛技術用在這些半成品上,讓這些零件在工廠內自動行駛到所需的區域,根據官方說法,在低速下穩定行駛的表現,已經跟輸送帶相同等級,如此一來能夠大幅減少生產線佈建成本,並增加靈活性。
用誇張一點的說法,他們可以在不同的地方組裝車輛的前段跟後段,然後這「兩段」會自己行駛到中段的組裝區域,在這裡進行合體,這顯然不是向特斯拉學習,靈感可能來自小丑巴其船長。
從他們展示的技術看來,Toyota 似乎將造車成本視為次世代電動車的決勝關鍵,因此使出渾身解數,要改良他們的製程。與此同時,特斯拉則是明確的將目標定在 2.5 萬美元的平價車,如果 Toyota 的研發速度夠快,雙方就有機會在 2027 年正面對決國民電動車這個終極戰場。
(圖片來源:Toyota)