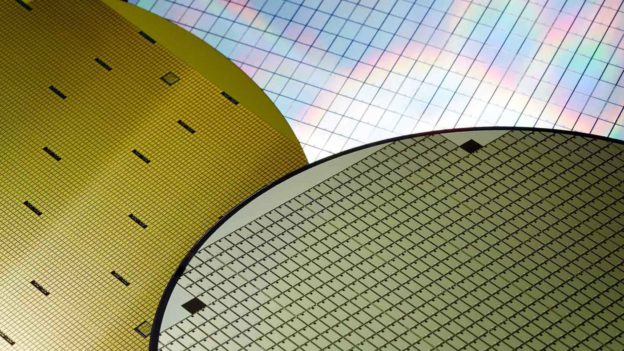
“不同產品與製程,對粗糙度要求相異甚大,將影響後續鍍膜的附著性。
量測粗糙度藉以製程改善方向有其必要,該如何選擇到位的分析工具呢?
一般普遍都曉得的觀念,在爬山、跑步等運動時所穿著鞋子底部、或是越野車輪胎的表面,都會採用粗大的顆粒來增加摩擦阻力,相反地在清潔用品或外套衣服上若是經過一些特殊的表面處理,能夠減少表面附著力,在經過液體沖洗潑灑後不致吸附表面。
這些都與表面粗糙與否有關。當然,在電子產品與半導體晶圓製造時的表面也均有粗糙度的要求,將會影響其後續製程如清洗的潔淨度、鍍膜的附著性、蝕刻的方向性等。
因此針對不同產品、製程或試樣,其粗糙度的要求也相異甚大。如晶圓或玻璃的表面,其平均粗糙度約在一奈米(1 nm)以下,而經過微蝕、清洗後,表面粗糙度稍微增加,如此可提高後續鍍膜的附著性。
在製程設備中裝載晶圓的載具,經過機台不斷重複運作,或與蝕刻液、鍍膜、機械等應力的交互作用的影響下,可能導致粗糙度是數十甚至數百奈米的變異。這樣的量測範圍與精度就並非在同一種儀器上可執行量測的,有時會受限於樣品的尺寸大小,不得不更換儀器來量測。
那麼,在各式各樣的產品裡,該如何挑選適當的量測工具呢?本期宜特小學堂,將與各位分享「如何借力三大工具,精準量測樣品表面粗糙度。」
表面紋路(Surface texture)的粗糙度(Roughness)定義
「真實的表面與完美水平面之間的垂直高度差」(參見圖一)。目前國際規範 ISO 與 ANSI 中明確定義的有所謂「算術平均粗糙度- Ra(Arithmetic average roughness,AA)」、「方均根粗糙度 – Rq (Root Mean Square roughness,RMS)」等等,均可以用於定義樣品粗糙度的大小與變化,提供製程改善的方向。
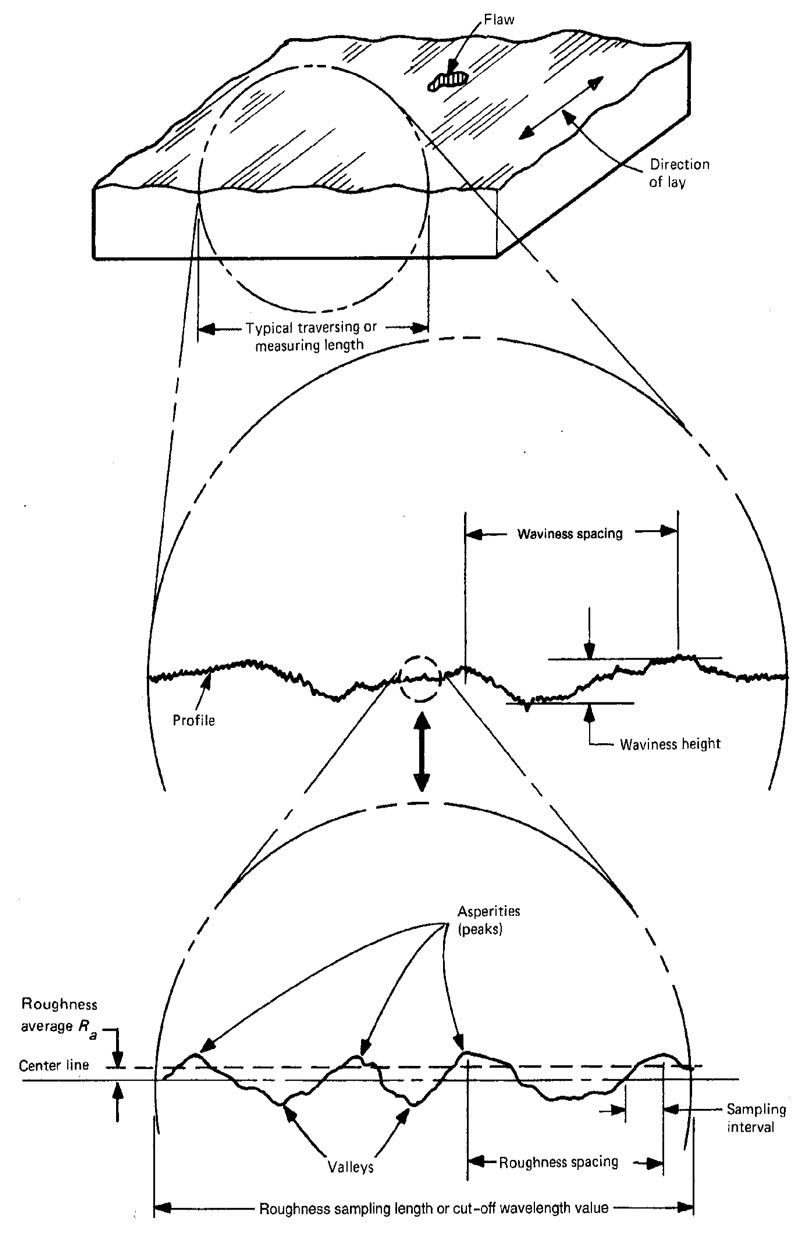
▲圖一:(圖片來源 ANSI / ASME B46.1, ASME, New York)
一、三大利器速得正確粗糙度數值
粗糙度傳統的量測方式,是採用一支鎢鋼針進行表面接觸方式的掃描(圖二),但受限針的曲率半徑較大,以及接觸的施力易刮傷樣品或造成形變等問題,僅適用於固體較硬的材質量測,或簡單的高度差量測(如表面形貌儀,Surface profiler / Alpha-Stepper),其他如半導體使用光阻、高分子類軟性的材料就無法使用了。
▲圖二: 探針曲率影響掃描形貌的真實性(圖片來源:Modern tribology handbook 2001 by CRC Press LLC)
宜特實驗室,提供了三種表面粗糙度量測的分析工具,包括白光干涉儀(White Light Interference,WLI)、原子力顯微鏡(Atomic Force Microscopy,AFM)與 X 光反射分析(X-Ray Reflectometry,XRR)
- 白光干涉儀(WLI):適用於大尺寸、非透光材料樣品
白光干涉儀 (WLI)是利用光學干涉的原理(圖三),在建設性干涉條紋的間距等於固定波程差,即可應用於計算高度,以形成表面高低起伏的立體 3D 形貌(圖四),並進而計算出粗糙度,因為是採用光學顯微鏡,適合應用在較巨觀的樣品上,如待測物尺寸大於一百微米(100 um)以上、甚至於數個毫米(mm)均可採用此方式量測。
WLI 大多應用在金屬或線路,以及塑膠等不透光材料的表面形貌量測,透光材料如玻璃等就不適用。或是若待測物在表面無法進一步鍍金屬來進行 WLI 量測時,就必須考慮使用其他分析技術。
圖五為金屬表面經過酸洗後的表面粗糙度量測約三百微米(300 um)見方的結果,平均粗糙度(Ra)在一微米(1 um)以上。
▲圖三: 白光干涉條紋
▲圖四: 3D表面形貌
▲圖五: 2D / 1D表面形貌與分析粗糙度Ra數值
2.原子力顯微鏡(AFM):適用於晶圓及玻璃材料樣品
原子力顯微鏡(AFM),是使用奈米等級的矽探針進行掃描以取得表面高低起伏的形貌,可針對極平坦的樣品、或高分子軟性材料(如: 光阻)進行表面粗糙度量測,常應用於晶圓與玻璃清洗、鍍膜或蝕刻前後等這類表面數十微米範圍的微觀分析。
近年來更大量運用在積體電路上化學機械研磨(CMP)、線路重布(RDL)與凸塊下金屬化(UBM)製程,相關的研究均使用 AFM 在蝕刻製程的前、後表面做量測監控,如果粗糙度異常將會導致後續覆蓋薄膜的剝落甚至是可靠度的問題發生。
如圖六為高分子材料聚醯亞胺(PI)二微米(2 um)見方的表面形貌,平均粗糙度(Ra)僅約八奈米(8nm)。為了進行實驗前、後的比較,必須在不破壞晶圓片的狀態下做量測,因此 AFM 設備的規格除了提供基本的量測外,待測樣品的載具台,必須達十二吋,方能滿足十二吋晶圓的量測需求。
▲圖六: AFM 量測表面形貌與分析粗糙度 SAD 百分比、Rq 和 Ra 數值。
3. X 光反射分析(XRR) :適用於多層膜、極薄膜樣品
X 光繞射分析(XRD)設備有搭載薄膜 X 光反射率(X-ray Reflectivity,簡稱 XRR)分析的功能。XRD 是運用繞射原理,而 XRR 則是 X 光的反射法,透過全反射光譜與分析軟體擬合的方式得到粗糙度,適用在極薄膜(Ultra-Thin film)。當總膜厚在五百奈米(500 nm)以下,可用此分析得到粗糙度、以及厚度(Thickness)與電子密度(Density)等相關資訊。
XRR 最特殊的是當樣品為多層膜(Multi Layers)時,除了得到表面最上層的粗糙度外,亦可得到膜與膜層或是膜於基材之間的介面粗糙度(Interface roughness),這部分是前兩種工具 – WLI 與 AFM 所無法直接量測的。此外在材料的方面並無結晶與否的限制,即使是非晶質的有機材料,都可以應用 XRR 來量測。
不過因為是採用光反射原理,薄膜表面平均粗糙度還是有其要求,如果大於 5 nm 即不適用了。
現今,半導體製程上使用越來越多屬於奈米等級的薄膜,如圖七,為厚度僅約 7 nm 的氧化鋁薄膜鍍在矽晶圓上,表面粗糙度約五埃(0.5 nm),矽晶圓與氧化鋁的介面粗糙度約二埃(0.2 nm),這都可以很快地不破壞樣品而經由 XRR 分析得知,若用一般的 AFM 顯微鏡是完全無法得到厚度。
▲圖七: XRR 擬合分析氧化鋁薄膜的厚度、粗糙度與密度。
二、一表參透三大粗糙度分析利器特性
以上三種粗糙度分析,樣品均不需要進入真空系統,因此大部分樣品均可直接分析,分析完仍可進行後續的實驗,不會破壞樣品。最後下表為上述三種量測設備的特性比較,可以針對欲進行樣品尺寸的要求與粗糙度量測的範圍,選擇最合適的設備來獲得最有效的數據分析。
▲表一: 表面粗糙度分析工具比較表
本文與各位長久以來支持宜特的您分享,若您有相關需求,或是對相關知識想要更進一步了解細節,歡迎洽詢 +886-3-579-9909 分機 1068 邱小姐 │ Email: marketing_tw@istgroup.com。
您可能有興趣的相關文章
(圖片來源:宜特科技)