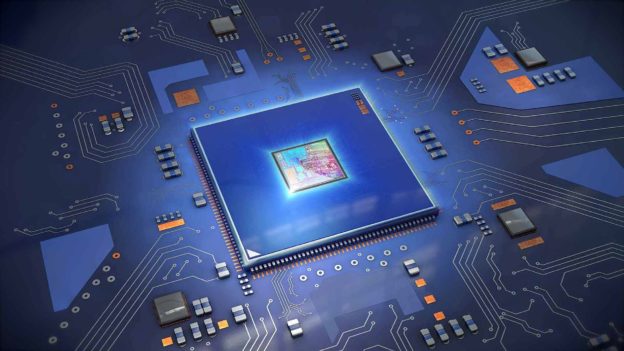
IC 晶片本身可靠度沒問題,組裝於 PCB 時卻出現 Fail,原來是錫球焊接出了問題,如何預防?
過去,IC 設計廠商送產品進行檢測時,通常只有針對元件,元件測試雖沒有問題,但組裝於印刷電路板(PCB)時,卻發生問題,以致於產品必須重新送回檢測,費時又費力,也支付更多附加成本,造成上述問題的起因在於,IC 元件廠商並不了解元件到了封測廠或系統整合商手中時,會因封裝或黏合過程中造成如何的影響,加上本身並不製造印刷電路板,對此技術不了解,以致於無法符合系統廠商的要求;為了讓 IC 元件更貼近實際使用環境,板階可靠度(Board Level Reliability, 簡稱 BLR)測試應運而生。
何謂板階可靠度(Board Level Reliability, BLR)
板階製程又稱 L2、Level2 或 Board Level 2,也就是將第一層級封裝後的 IC,組合至 PCB 上之製程。而所謂的板階可靠度(BLR),就是驗證 IC 元件上板至 PCB 之焊點強度(Solder Joint)的測試方式(圖一)。
▲圖一:板階可靠度焊點強度
這項試驗,在宜特科技可靠度驗證實驗室已經運行十多年,亦是目前消費型電子產業常規的測試項目,而隨著汽車電子系統的複雜度提升,更多的元件和模組被運用在汽車內,BLR 遂成了車電系統的重要測試項目之一。
板階可靠度(BLR)測試是半導體資深工程師都知道的必測實驗項目,不過隨著越來越多新人加入半導體產業界,宜特科技可靠度驗證實驗室也時常接到客戶的詢問 BLR,該如何進行?有哪些測試項目?如何選擇測試條件?為了讓廣大客戶更了解此試驗,本期宜特小學堂,我們就來談談 BLR 測試吧!
一、 消費性 BLR 與車用電子 BLR 有何不同?
- 消費性電子 BLR 可靠度驗證
隨著消費性電子產品越趨複雜與製程能力大幅提升,所需的晶片種類增多,為了容納更多晶片並提升效能於手機的應用,晶片結構開始走向兩種趨勢,一是讓原有 IC 元件逐漸往輕、薄、短、小的趨勢發展,另一是將眾多 IC 組合再一起成為功能強大的晶片,但這會讓 IC 元件尺寸放大好幾倍,導致封裝技術也必須隨需求而轉變,造成這些晶片與印刷電路板結合後的可靠度必須重新被驗證。終端國際品牌大廠為了管控零件品質,則會直接要求晶片供應商執行 BLR 測試。以手機的使用環境考量,晶片與印刷電路板結合後所須被檢視的項目中,最重要的乃機械應力與環境應力,例如摔落實驗與溫度循環實驗等。
而板階可靠度在消費性產品的國際規範可參考 JEDEC B102/ B103/A104/B111/B113 IPC-9701~9704/9708 或是各家終端消費型品牌大廠包含手持式產品、車用電子等類型也都有各自訂定的客戶規範。
- 車用電子 BLR 可靠度驗證
隨著汽車電子系統的複雜度提升,更多的 IC 元件被運用在汽車內部,車用元件上板後的焊點可靠度驗證,也就是 BLR,遂逐步成為車電重要測試項目之一,不僅 Tier 1 模組廠對此制定專屬驗證手法,令人注意的是 AEC 汽車電子協會於 2018 年出爐的 AEC-Q104,明確定義了車用電子的板階可靠度試驗(Board Level Reliability)項目,雖然項目僅有溫度循環(BLR TCT)、落下(Drop)試驗,但只針對 MCM(Multi-Chip Modules),並未將較普及的封裝形式一同納入,較未能完全貼近 Tier 1的客戶規範,不過也是車用板階可靠度通用標準發展的一大步,相較於去年開始車市的火熱與缺料的議題發生,AEC 汽車電子協會是否有更進一步更新 AEC-Q104,是值得我們期待的。 (延伸閱讀: 進入電動車供應鏈必備-國際可靠度品質車規五步驟一次解析)
- 消費型電子產品 Board Level 測試條件,是否可以參考或沿用至車用產品?
答案是不行的,因為這些系統模組導入車輛設計之中,車載平台使用的環境與結構大不相同,汽車在啟動後,所有晶片都會開始承受振動、機械的應力與外在惡劣環境,若使用消費型電子產品測試條件後,在真實使用環境可能會發生所謂的早夭現象。宜特板階可靠度實驗室以 JEDEC 和 AEC-Q 與常見的客戶規範,進行比較(表一),讓您一目了覽差異在哪裡。
▲表一:消費型與車用 BLR 的規範差異
二、板階可靠度(BLR)測試如何開始進行?
在正式進入板階可靠度 BLR 測試之前,必須先經過測試版的設計、製作、SMT 組裝等,才進入正式的可靠度試驗;在試驗後,更需進行故障分析,找到失效位置,進而計算出產品壽命,接下來,我們將簡單介紹各項流程與步驟(圖二)。
▲圖二:BLR 試驗步驟
- 第一步驟: PCB 測試版設計與製作
BLR 測試,就是須了解元件上板後的焊點品質,第一步,需要進行 Daisy Chain(菊花鍊)設計(圖三),將您的待測樣品元件與電路板連結的各個焊點形成網絡,藉此即時監控每個焊點良率,可有效得知各個錫球焊點是否失效,更能準確擷取失效的時間點,及早進行改善。
▲圖三:Daisy Chain 設計
宜特板階可靠度實驗室除了提供符合 JEDEC/IPC 規範的 PCB 測試版(圖四),亦可提供特殊設計的印刷電路板,讓您的IC可直接在模擬系統廠商的 PCB 板上測試,有效防止不可預知的異常狀況。
▲圖四:宜特科技可靠度驗證實驗室可提供符合 JEDEC/IPC 規範的 PCB 測試版
- 第二步驟:SMT 表面黏著製程
表面黏著(SMT)製程是板階可靠度測試(BLR)的第二關卡,將元件上板至測試版。而 IC 黏著在模擬 PCB 上的品質好壞,將直接影響到產品壽命判斷精準度。品質好壞的關鍵因素包括,錫膏特性、印刷條件設定(如脫模間距、脫模時間、印刷速度)、置件精準度、鋼板選擇。
SMT 後,就是透過 X-ray 或超音波檢查迴焊(Reflow)品質,確認錫球黏著狀況。
特別說明,為了有效進行 RA,宜特建議在 SMT 之前,就先進行元件與 PCB 來模擬翹曲的程度,再去調整 SMT 的參數設定,確保 SMT 過程中有良好的焊接品質,如此可避免因不良焊接品質導致影響可靠度驗證以及不必要的成本開銷。
量測分析的速度非常快,約一小時就可得知元件在不同溫度的變形量,也能模擬溫度循環的環境,協助您在後續可靠度測試進行搭配,觀察產品在哪個溫度會達到最大的變形量(圖五),並能在測試中思考如何改善與預防。(延伸閱讀: 掐指算出 Warpage 翹曲變形量 速解 IC 上板後空焊早夭異常)
▲圖五:模擬溫度循環環境,觀察產品在哪個溫度會達到最大的變形量
- 第三步驟: 正式進入可靠度試驗
BLR 試驗,主要分為兩大項目,包括低應變率試驗與高應變率試驗,這兩大項項目又細分好幾項試驗,試驗目的最主要就是試驗在不同的情況之下與測試版連接的焊點強度。
低應變率試驗(Low Strain Rate Test)
意旨較低、較慢的變化,也就是所謂的耐久性試驗,包括溫度循環/溫度衝擊試驗(Temperature Cycle Test, 簡稱TCT)、板彎/彎曲試驗(Bending)等。
高應變率(High Strain Rate Test)
意旨樣品在較短時間內遭受到劇烈變化,包括機械衝擊試驗(Mechanical Shock)、振動試驗 (Vibration)等。
- 第四步驟:板階可靠度後的整合故障分析
當元件上板後進行一系列的可靠度驗證,可靠度驗證過程中產品失效時,透過板階整合故障分析能快速將失效介面找出,將可協助您釐清真因後,能快速改版重新驗證來達到產品通過驗證並如期上市。宜特科技透過板階整合故障分析來定位,並協助您找出失效介面的方式包括:
- X射線檢測(2D & 3D X-ray):以非破壞的方式確認產品在測試後是否有介面異常超音波掃描(SAT):以非破壞的方式確認產品在經過BLR測試後是否有脫層
- Thermal EMMI:藉由Thermal EMMI 定位因試驗後所產生的Defect位置
- 紅墨水試驗(Dye and Pry)確認 PCBA,是否出現焊點劣化情形(Micro-crack)
- 研磨處理服務(Cross-section):切片檢查特定區域介面是否有異常(圖六/圖七)
▲圖六:經過機械衝擊試驗高速衝擊,藉由 Cross-section 檢測,發現樣品材料內部受不了衝擊,進而錫球接合位置產生裂縫(藍箭頭)。
▲圖七:經過溫度循環,長時間熱漲冷縮後,藉由 Cross-section 檢測,發現樣品材料產生裂痕(藍箭頭)。
三、常見板階可靠度測試問題
最後,宜特板階可靠度實驗室,統整近年來,客戶時常提出三大疑問。
- 經過了 1,000 個溫度循環測試實驗,能代表些什麼呢?
1,000 個循環,意旨一千個工作天,也就相當於接近三年的使用時間,所以經過 1,000 個循環就可以說,可以保障產品至少兩年到三年的使用時間不會故障。
- 板階可靠度中的機械衝擊試驗(落下測試),該如何選擇條件?
每一種元件會應用到的地方不盡相同,例如用在手機、電腦或平板上,所以能夠承受掉落高度的衝擊也不相同。舉例而言以手機來說,就是以 112 公分來模擬從手上掉下來的高度,對應下表二,相對應的條件就是 Condition B 1,500G, 0.5ms。
▲表二:落下測試試驗條件
- BLR 得到的數據如何推估實際產品壽命?
歷經長時間測試後,得到樣品一定數量的失效數據,進一步的使用韋伯分析(Weibull)進行推估計算該產品特徵壽命( η ),無論是在產品驗證階段或研發中的驗證,都可透過 Weibull 探討產品是否可以承受可靠度驗證,或已具有足夠可靠的使用壽命。
以圖八為例,縱軸為失效百分比、橫軸為測試時間,在相同的測試環境與測試時間中,就明顯的發現兩者巨大落差 2,000 循環的特徵壽命,單單只是更換一種材料就造成了如此巨大的改變,由此可見在可靠度測試中材料的選用與應用非常的重要,些微的前段差異可能就會導致後段重大的落差。
▲圖八:材料一(藍線):η= 3,506 cycles;材料二(黑線):η= 5,586 cycles
本文與各位長久以來支持宜特的您,分享 BLR 經驗,宜特提供一站式的板階可靠度試驗,不論從測試板的設計、製作、SMT 組裝、可靠度測試、失效分析都擁有豐富的經驗,若您有相關需求,或者對相關知識想要更進一步了解細節,不要猶豫,歡迎洽 +886-3-579-9909 分機 1068 邱小姐│ Email: marketing_tw@istgroup.com。
(圖片來源:宜特科技)