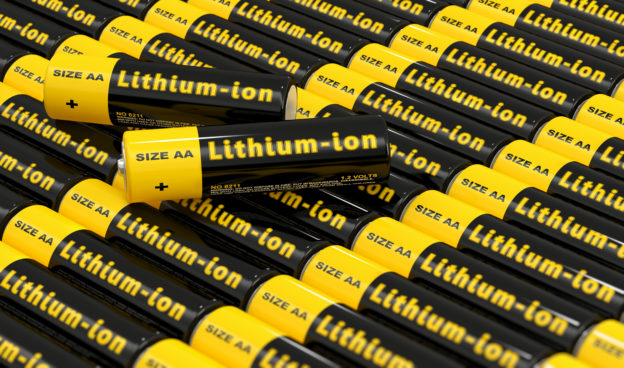
因應電動車的蓬勃發展及鋰電池正極材料大量需求,工研院投入將廢棄鋰離子電池的黑粉,提純成為價值較高,且純度較高的硫酸鈷、氧化鈷,可作為鋰電池正極材料的化工原料。為期 3 年,已獲得關鍵技術,並達到試量產的階段。
工研院研發鋰離子電池回收技術,再生料每公斤價格增加 10 倍 |
作者
Daisy Chuang |
發布日期
2022 年 01 月 18 日 16:00 |
分類
會員專區
, 能源科技
, 鋰電池
| edit
![]() ![]() ![]() ![]()
Loading...
Now Translating...
|
因應電動車的蓬勃發展及鋰電池正極材料大量需求,工研院投入將廢棄鋰離子電池的黑粉,提純成為價值較高,且純度較高的硫酸鈷、氧化鈷,可作為鋰電池正極材料的化工原料。為期 3 年,已獲得關鍵技術,並達到試量產的階段。
文章看完覺得有幫助,何不給我們一個鼓勵