
汽車的發源地位於德國南部的斯圖加特,這裡除了是第一輛汽車的誕生處,也是賓士汽車總部所在地,就在斯圖加特郊區,座落著賓士最先進也最神祕的 56 號工廠,所有賓士的頂級車,都在這裡生產。
從斯圖加特往西約 20 公里,我們來到全世界最大的賓士基地,辛德芬根(Sindelfingen)這座城鎮幾乎就是為了賓士而存在,面積將近 300 萬平方公尺的廠區,相當於 228 個巨蛋球場,如果你錯過了前往此處的交流道,別擔心,光是這個廠區就有三個高速公路交流道。
廠區內有多達將近 4 萬名員工,光是停車位就有 1.7 萬個,裡面有自己的醫院,多達 6 棟員工餐廳,甚至有自己的消防隊,擁有 25 輛消防車,就連火車站也有鐵軌直接進到工廠裡,可以快速將車輛送到其他地區。
▲ Factory 56 工廠屋頂滿是太陽能板,廠內電力有 35% 都來自這裡。
在這個碩大的生產基地內,有兩個地方藏著賓士的最高機密,分別是軟體中心和 56 號工廠(Factory 56),這兩個地方禁止任何媒體拍攝、錄音、錄影,因為這裡不僅是賓士的驕傲,也是他們的未來命脈,這篇文章要介紹的正是賓士 56 號工廠,全世界所有的 S-class、EQS、Maybach 和防彈賓士車,都在這裡製造。
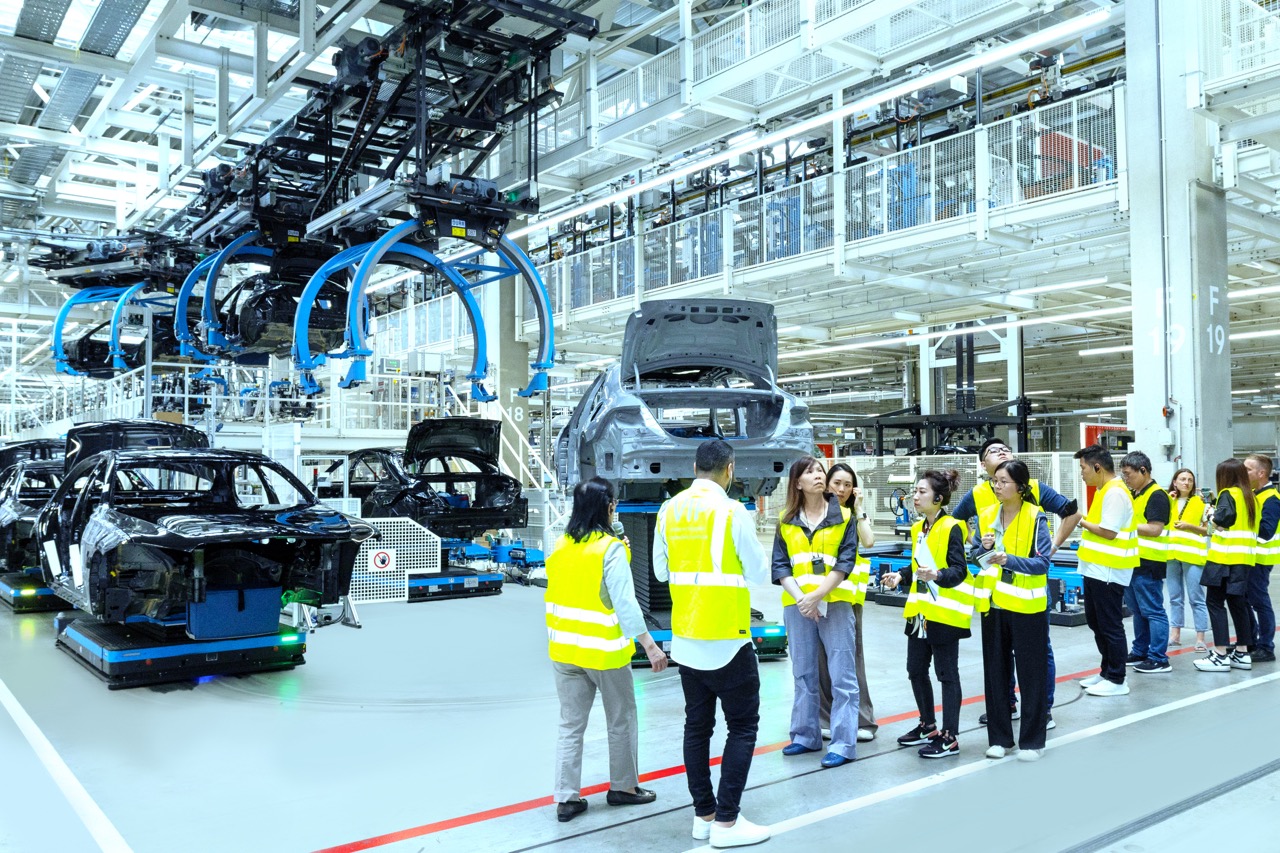
▲我們這群來訪的媒體是廠內唯一需要穿反光背心的高危險族群。
Factory 56 於 2020 年正式啓用,占地 22 萬平方公尺,相當於 520 個籃球場,共有 2 千名員工,擁有最先進的工業 4.0 生產技術、5G 連線、自動化運輸系統和 AVR 輔助和 5 千台以上的機器人與機械手臂,然而最讓人驚訝的是,這個高科技工廠對人工的仰賴程度高到不可置信。
以人為主的智慧工廠
說到智慧製造,很容易想到無人工廠或是關燈工廠,但在這裡卻完全不是這麼一回事。56 工廠不僅燈光明亮,屋頂甚至有非常多天窗,導入大量自然光,員工只要抬頭就能看見藍天。做為年產量約 15 萬輛的工廠,這裡不僅一點臭味都沒有,甚至非常涼爽,員工也不需要戴安全帽,唯一穿著反光背心的人,只有我們這群外來訪客。
「這裡的員工都是週休二日,並且只有早班和晚班,一班 8 個小時,外加 1 小時午休,每 90 分鐘休息一次。」Factory 56 發言人麥斯那(Sebastian Messner)表示,想要打造出最好的車輛,最終還是必須依靠最優秀的工人,因此讓工人開心,是這個工廠的設計核心。
▲ 移動式車身吊架可以旋轉,讓員工輕鬆安裝 EQS 的電動馬達。
更讓人意外的是,與一般工廠的流水線作業不同,在 56 工廠內,每 90 分鐘的休息時間過後,員工就要調換工作位置,原本組裝輪圈的人,可能就要換去裝電池,一天之內就要負責 6 種不同的零件。透過這種輪調方式,員工不會精神疲乏,或許這也是我們難得在參觀工廠時,可以看到工人笑著跟我們打招呼的原因,即便我們擋住了他們的動線。
有人就有失誤,但賓士做出一套零失誤產線
56 工廠內生產的每一輛車,都要經過 900 個以上的生產站,每個站裡的工人又一直輪調,不僅如此,在相同的一條產線上,前一台組裝可能是要送來台灣的純電 EQS,下一台則是右駕的燃油引擎 S400,聽起來像是大量組裝失誤的高風險集合,但賓士的厲害之處也在此展現。
▲ 正在安裝 EQS 電池組的這位員工,接下來可能要安裝燃油車的傳動系統。
「在這裡我們稱之為零失誤系統,不同的員工、不同的車款、不同的市場需求,我們都可以讓組裝零失誤。」麥斯那指著各條生產線旁的貨架說,這套系統的核心就展現在這個「零件超市」。
工廠裡面有 440 台的無人運輸車(AGV),他們負責將零件送到每個工作站,讓工人可以完成組裝,當 AGV 接獲任務來到零件超市時,零件貨架上的指示燈就會亮起,負責取貨的工人就能夠準確地找到所需的零件,如果拿取的數量、品項有誤,貨架就會亮紅燈,確保正確。當 AGV 獲得了它這次需要的所有零件,它就會自己開往工作站,若有錯誤,它也會亮紅燈提醒工人檢查。
▲ 載好零件的 AGV 正在前往組裝站。
所有的 AGV 一次只做一件事,當它抵達工作站時,工人不需思考他要拿什麼,全部拿出來就對了。同樣地,在工人完成組裝任務時,他的零件抽屜必須是空的,只要有剩餘零件,就代表組裝有缺漏,可以立刻修正。
這套系統背後的靈魂,是賓士自行開發的 ERP 資源管理系統,搭配他們按時生產、依序組裝的原則,告訴所有站點和 AGV 相關任務。而每一項零件、每一個站點都有專屬的識別條碼,透過廠區內的 5G 通訊網路,用最快的速度彙整到系統內,讓所有工作程序完美無誤。
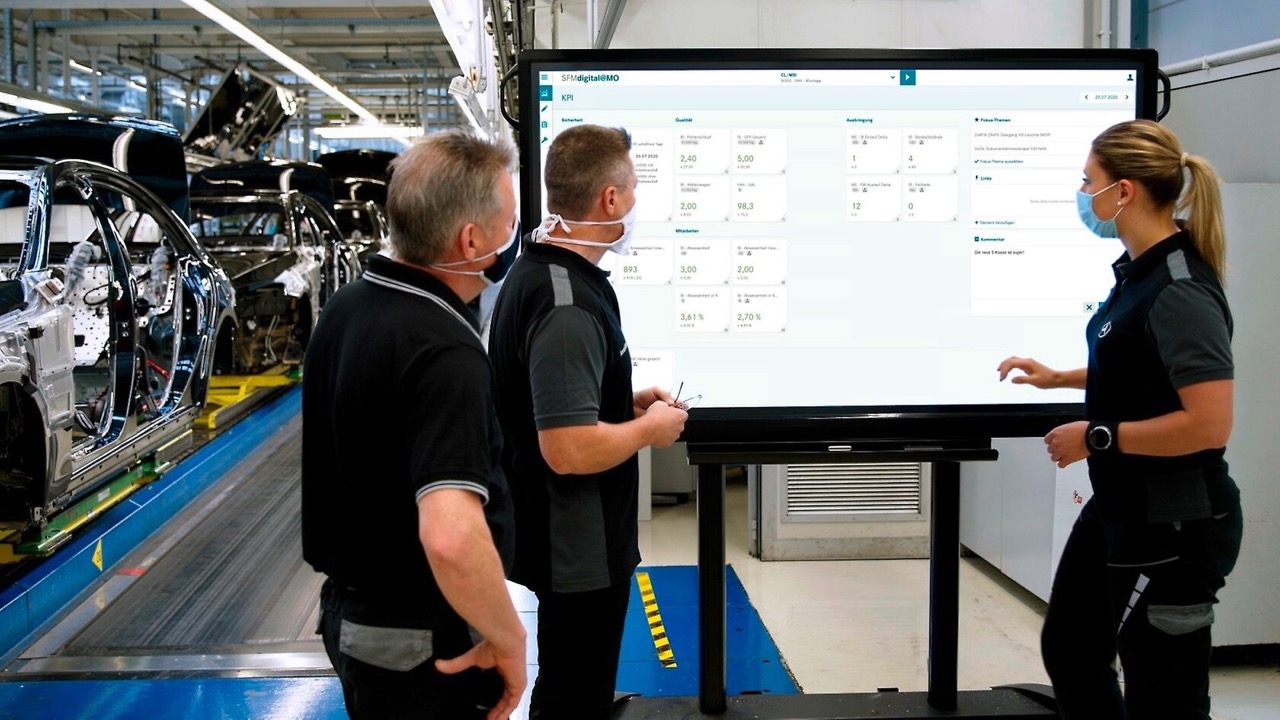
▲ 每一個零件、每一個步驟全都數位化管理,靠的就是自家的 ERP 系統。
家裡開工廠的朋友,肯定想到一些問題,例如:供應商缺料怎麼辦?對 56 工廠來說,要成為這裡的供應商,就必須有一定的覺悟。為了避免運輸過程的意外,所有供應商必須在 56 工廠附近設置備料倉庫,時間到就必須出貨,萬一倉庫沒有備料呢?「供應商必須用直昇機,將零件送來工廠」,麥斯那說,這就是賓士對供應商的要求。
賓士的要求:完美
賓士不僅對供應商有嚴格要求,對自己也是一樣。即使有強大系統支持,賓士依然在產線上配置檢查點,每經過 5~6 個組裝站點,就會有一位品管人員,拿著平板電腦核對,確保沒有問題才放行。而賓士最病態的要求,就在產線的最末端。
▲ Factory 56 內每個工作區都至少有一位女性,圖中員工正在透過平板檢查組裝是否正確。
當整車組裝完成後,車輛會進入一個由 4 座機械手臂包圍的檢查區,這些機器人是世界上最龜毛的檢測員,手臂前端的雷射會在 90 秒內掃描全車的所有接縫,確保每一輛車的公差都符合標準。56 工廠對於公差的要求也有一個絕對值:0.0 公分。
當機器人發現公差後,就會在系統內標記位置和公差大小,在下一個站點,就有一群員工開始對車輛上下其手,消除所有公差,經過大約 10 個站點,這些公差就會徹底消失。
接著會有員工上到駕駛座,將車開到最後的檢驗區,確保所有功能都正常,然後再交給最後的品管員,他會用手撫摸整輛車身,試圖找出機器無法檢測出的瑕疵。
更快的龜毛、更靈活的保守
如果要用一句話來形容 56 工廠,我想就是「用一樣的挑剔標準,更快的完成更複雜的工作」,在這裡我們看見賓士對於組裝品質的不妥協,但為了能夠靈活快速的生產出世界各地所需的車款,因而打造出這樣一套複雜卻又精準無誤的產線。
▲ 在此生產的每輛車,組裝時的數據會保存 25 年,包括每個螺絲的扭力、車漆厚度和零件資料等。
因為賓士非常清楚,隨著電動車時代來臨,他們的產品更新速度必須更快,生產線必須更加靈活,才能維持競爭力,而不再是過去的三年一小改、八年一大改。
這樣的產線設計雖然令人佩服,但也不得不讓人擔心,為了達成最高規格的品質要求,製造成本水漲船高,超過一百年的品牌榮耀,也是賓士在面對變革時最沉重的負擔。
(圖片來源:Mercedes-Benz 提供)